Science Behind Anti-Glass Fiber Exposure Agent: A Deep Dive
When glass fiber is incorporated into materials such as nylon and polyester, it dramatically enhances their mechanical properties. However, a significant challenge arises: glass fibers can often “float” to the surface, leading to product defects like rough surfaces, poor aesthetic finishes, and compromised structural integrity. In industries such as automotive, and construction, where reinforced plastics are crucial, this problem can undermine both the quality and performance of the final products. But what if there was a solution that could effectively address this issue while enhancing the material’s overall properties? Enter the Anti-Glass Fiber Exposure Agent, a revolutionary solution designed to improve the compatibility and performance of glass fiber-reinforced polymers.
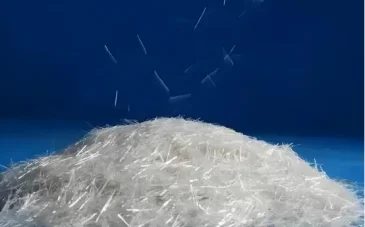
What is an Anti-Glass Fiber Exposure Agent?
An Anti-Glass Fiber Exposure Agent, specifically UniMax D56, is an innovative processing aid used in the plastics and plastic alloys industries. This agent is specially formulated to solve the common problem of glass fiber exposure during the production of glass fiber-reinforced nylon and polyester products. The UniMax D56 serves multiple purposes: it promotes dispersion, enhances compatibility, acts as a coupling agent, and provides lubrication. These benefits not only prevent glass fiber exposure but also improve the overall mechanical properties, flowability, and surface gloss of the final product.
UniMax D56 is a partial amide derivative of a low molecular weight acrylic long-chain alkyl ester copolymer. Its creation involves high-temperature oxidation polymerization technology, making it particularly effective for reinforcing plastics such as glass fiber-reinforced nylon and polyester. By improving the interface bonding strength between glass fibers and resin, the agent mitigates the problem of glass fiber exposure, which is prevalent in industries using reinforced thermoplastics.
The Key Functions of Anti-Glass Fiber Exposure Agents
Dispersion: Ensuring Uniform Fiber Distribution
The UniMax D56’s molecular chain is equipped with carboxyl groups, amide groups, and non-polar long-chain alkyls. The carboxyl groups enable it to react with the surfaces of both nylon and polyester resins as well as the glass fibers, thereby promoting in-situ grafting. This reaction activates the surface of the glass fiber, improving the adhesion between the fiber and resin. As a result, the glass fiber becomes well-dispersed throughout the resin, preventing clumping and ensuring that the final product benefits from an even distribution of fiber reinforcement. This uniform dispersion is critical for improving the mechanical strength and stability of composite materials.
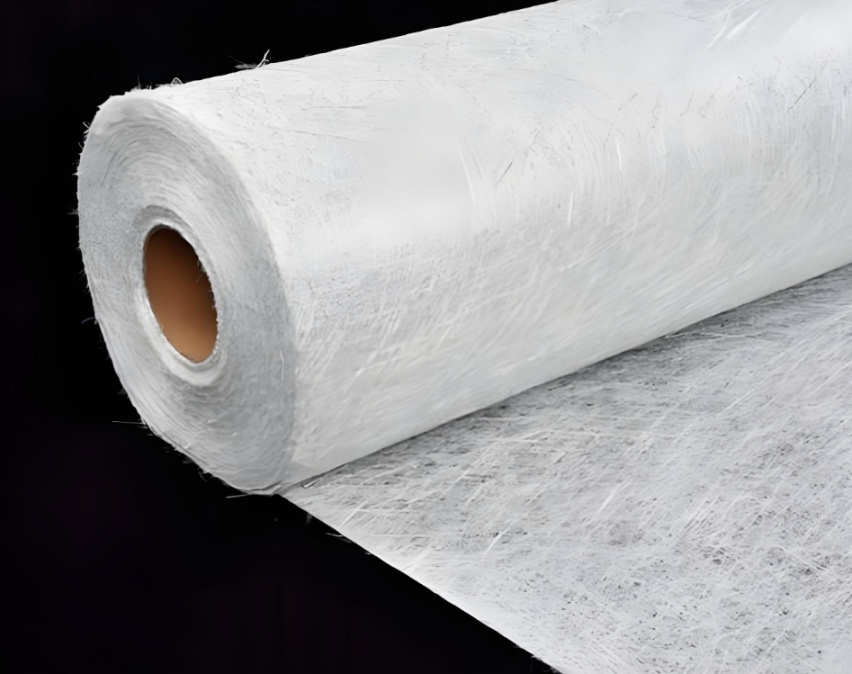
Compatibilization: Enhancing Fiber-Resin Interaction
The presence of the amide group within UniMax D56 contributes to its excellent compatibility with both nylon and polyester. This compatibility ensures that the glass fibers and resin blend seamlessly, enhancing the structural integrity of the composite. By facilitating better fiber-resin interaction, UniMax D56 enhances the strength and durability of the end product, making it more resistant to environmental stresses such as heat, chemicals, and mechanical wear.
Lubrication: Improving Process Efficiency
Another essential feature of the UniMax D56 is its non-polar long-chain alkyl component. This element provides lubrication, reducing the friction between the polymer melt and the hot metal surfaces in processing equipment. As a result, manufacturers experience smoother processing, which can lead to increased production speeds, reduced wear on machinery, and better overall product quality. Additionally, this lubrication aids in improving the surface finish of the molded parts, contributing to an aesthetically appealing final product.
The Advantages of UniMax D56 in Industrial Applications
Improved Compatibility and Dispersion
One of the standout features of UniMax D56 is its ability to significantly improve the compatibility of glass fiber with both nylon and polyester. By enhancing the interaction between the resin and the fiber, the product promotes the efficient dispersion of the glass fibers, which is vital for ensuring consistent mechanical performance across the final product. This benefit is especially crucial in industries where high-strength composites are used, such as automotive and construction materials.
Enhanced Surface Finish and Gloss
UniMax D56 does more than just improve the mechanical properties of reinforced plastics. It also contributes to a superior surface finish by preventing the glass fibers from being exposed to the product’s surface. This results in a smoother, glossier appearance, which is essential for many high-end applications. For example, in automotive manufacturing, a glossy, smooth surface is a desirable characteristic for both aesthetic and aerodynamic purposes.
Stability and No Migration
Unlike many additives that may migrate or precipitate over time, UniMax D56 is designed to remain stable throughout the product’s lifecycle. This means that the additive will continue to provide benefits without altering the properties of the composite material over time. The stability of UniMax D56 ensures that the glass fibers remain effectively dispersed within the resin, maintaining the desired mechanical properties, appearance, and performance.
Enhanced Mechanical Properties
The combination of improved fiber dispersion, better adhesion between glass fiber and resin, and reduced friction during processing leads to enhanced mechanical properties. These include increased tensile strength, better impact resistance, and improved dimensional stability. For industries that rely on the strength and durability of composite materials, such as automotive, and construction, UniMax D56 offers a significant advantage in terms of both performance and product longevity.
The Role of UniVOOK Chemical in the Development and Supply of UniMax D56
UniVOOK Chemical, a leading producer and global distributor of industrial specialty chemicals is the supplier of UniMax D56. Based in Shanghai, China, the company has built a reputation for developing and manufacturing high-quality, reliable chemical solutions across a range of industries. With over 15 years of experience, UniVOOK Chemical has established a strong presence in global markets, supplying a diverse range of specialty chemicals, including epoxy-modified polyethylene wax, resin additives, and water treatment agents.
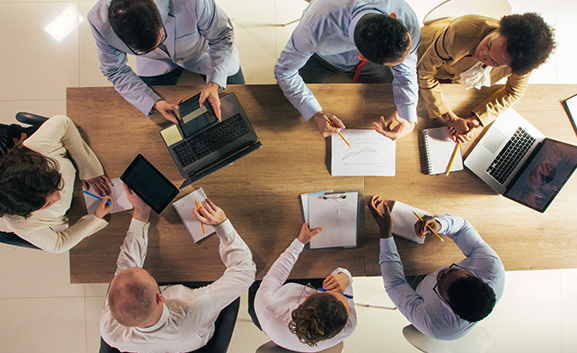
UniVOOK Chemical’s commitment to research and development (R&D) ensures that its products meet the evolving needs of industries such as pharmaceuticals, coatings, electronics, and food additives. The company operates three production sites and has a vast network of partners around the world, making it well-equipped to serve both local and multinational clients.
As a technology-driven company, UniVOOK Chemical invests heavily in cutting-edge R&D facilities and production technology, enabling them to stay ahead of the competition and provide customized solutions for their clients. With a highly qualified technical team, UniVOOK Chemical is able to tailor its products to meet the specific needs of various sectors, ensuring that its customers gain a competitive edge.
Why Choose UniMax D56 for Your Manufacturing Needs?
UniMax D56 is an essential tool for industries looking to enhance the performance and appearance of glass fiber-reinforced plastics. With its multi-functional benefits—improved dispersion, better compatibility, enhanced lubrication, and stability—it helps manufacturers overcome common challenges related to glass fiber exposure. Whether you’re in the automotive, or construction sector, the benefits of UniMax D56 are undeniable.
By partnering with UniVOOK Chemical, manufacturers gain access to not only a high-quality product but also a trusted supplier with a track record of excellence in the chemical industry. UniVOOK Chemical’s ongoing investment in technology and R&D ensures that UniMax D56 will continue to meet the demands of modern manufacturing, providing solutions that deliver superior results for glass fiber-reinforced composite products.
Conclusion
The introduction of the UniMax D56 Anti-Glass Fiber Exposure Agent marks a significant advancement in the world of glass fiber-reinforced plastics. With its unique blend of dispersion, compatibilization, and lubrication properties, this innovative agent addresses some of the most common and challenging issues faced by manufacturers in industries that rely on high-performance composites. By choosing UniMax D56, manufacturers can improve the mechanical properties, surface finish, and overall performance of their products—ensuring that they stay competitive in an ever-evolving market.
For more information and to explore tailored solutions for your specific industry, contact UniVOOK Chemical today.
About UniVOOK Chemical
UniVOOK Chemical is a leading provider of industrial specialty chemicals, offering custom manufacturing solutions and supply chain services to a global clientele. With a strong focus on R&D and innovation, the company develops and distributes advanced biochemical materials and chemicals for a wide range of industries, including pharmaceuticals, electronics, coatings, and high-grade cosmetics. With multiple production sites and a vast distribution network, UniVOOK Chemical is committed to delivering high-quality, reliable products to meet the evolving needs of industries worldwide.
Access Our Product Catalog and More to Discover High-Performance Chemicals Tailored to Your Business Needs