Epoxy-modified Polyethylene Wax: The Key Polymer Solutions
In today’s rapidly evolving manufacturing landscape, the need for high-performance materials that can seamlessly enhance product properties is more crucial than ever. But have you ever wondered how manufacturers achieve such remarkable material qualities like improved adhesion, better dispersion, and increased stability in composite materials? The answer often lies in specialized additives—one of which is Epoxy-modified Polyethylene Wax (GPW).
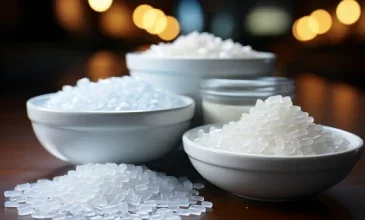
Epoxy-modified Polyethylene Wax is an advanced material that offers a range of functionalities in polymer-based systems. Obtained by grafting polar monomers containing epoxy groups to the molecular chain of non-polar polyethylene wax, this product brings together the best of both worlds—polar and non-polar characteristics. As a result, Epoxy-modified Polyethylene Wax exhibits excellent compatibility with both polar and non-polar polymers, making it an indispensable tool in various industrial applications. In this blog, we will explore the numerous needs this versatile wax addresses and the relevant solutions it offers across different industries.
The Science Behind Epoxy-modified Polyethylene Wax
Understanding the Composition and Properties of GPW
Epoxy-modified Polyethylene Wax is a modified version of polyethylene wax, designed by introducing epoxy-functional groups through a grafting process. This innovation allows the wax to possess polar characteristics due to the epoxy groups while maintaining the non-polar nature of the polyethylene wax backbone. The result is a hybrid material that offers an ideal balance between polar and non-polar interactions.
This unique structure endows Epoxy-modified Polyethylene Wax with several critical properties:
Good Compatibility: It shows excellent compatibility with a wide range of polar and non-polar polymers, making it a versatile solution for many applications.
Light Color and Low Odor: It is characterized by a clean, almost colorless appearance and minimal odor, which is ideal for consumer-facing products where aesthetics and sensory attributes are important.
Low Free Monomer: The product contains minimal free monomer, which reduces the risk of unwanted reactions during manufacturing processes.
High Thermal Stability: Epoxy-modified Polyethylene Wax remains stable under high temperatures, ensuring it performs well even in demanding processing environments.
Application of Epoxy-modified Polyethylene Wax in Polymer Processing
How GPW Optimizes Compatibility and Performance
One of the key applications of Epoxy-modified Polyethylene Wax is as a coupling agent in the production of various polymers. Its ability to enhance the compatibility between polymer matrices and fillers makes it particularly useful in the processing of polyethylene (PE), polypropylene (PP), and polyvinyl chloride (PVC).
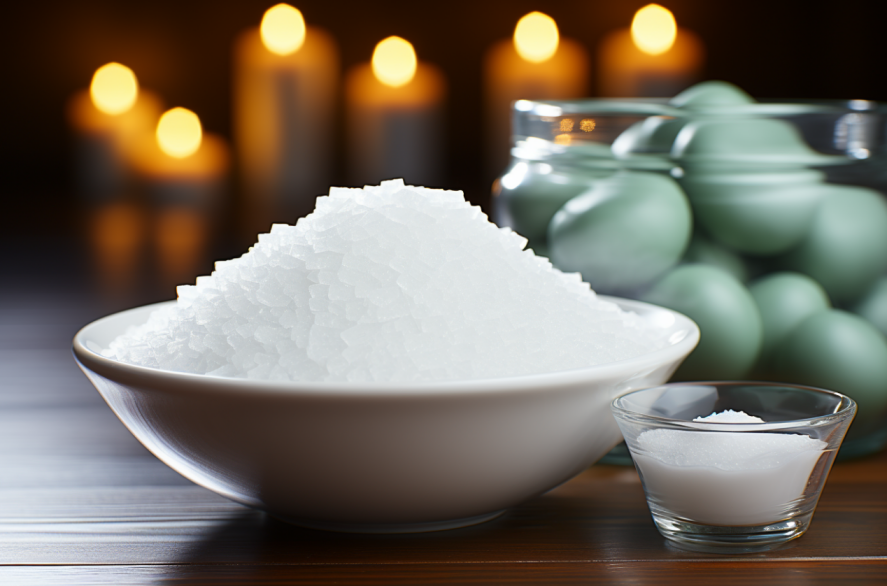
Coupling Agent: Enhancing Polymer-Filler Interaction
Epoxy-modified Polyethylene Wax acts as a coupling agent that facilitates stronger interactions between the polymer matrix and inorganic fillers. When fillers such as glass fibers or mineral powders are added to polymers, they often struggle to bond effectively with the non-polar polymer chains. Epoxy-modified Polyethylene Wax, with its polar functional groups, improves adhesion and helps in distributing these fillers more uniformly, leading to better mechanical properties, enhanced thermal resistance, and overall composite material performance.
This coupling effect makes Epoxy-modified Polyethylene Wax highly beneficial in industries where reinforced polymer composites are essential, such as automotive, construction, and electronics.
Dispersant: Promoting Uniform Distribution in Masterbatches
Epoxy-modified Polyethylene Wax is also widely used as a dispersant in the production of masterbatches. Masterbatches are concentrated mixtures of pigments, additives, and fillers that are later diluted into the final polymer product. In this process, achieving uniform dispersion of pigments, dyes, or flame retardants is crucial for the performance and quality of the final product.
As a dispersant, Epoxy-modified Polyethylene Wax promotes the even distribution of these ingredients within the resin. It reduces agglomeration and ensures that the pigments or additives are well-dispersed throughout the polymer, resulting in superior color consistency, better processing behavior, and improved product performance.
Polymer Compatibility: A Solution to Blending Different Materials
Bringing Together Different Polymers for Enhanced Properties
Another vital application of Epoxy-modified Polyethylene Wax is as a compatibilizer. It improves the interaction between incompatible polymers or between different phases of a polymer blend, enabling the production of high-performance alloys. This application is particularly important in the manufacturing of multi-polymer systems like PE/PP, PBT/PET, PA6, and PC alloys.
Compatibilizing Agent: Enhancing the Properties of Polymer Blends
In polymer blends, the different materials can often struggle to form a cohesive, stable system. Epoxy-modified Polyethylene Wax helps to bridge the gap between different polymers, improving the interface strength between the matrix phase and dispersed phase. This enhanced compatibility results in better mechanical performance, better thermal stability, and reduced phase separation, making it ideal for industries that rely on multi-component systems, such as automotive and packaging.
Industrial Lubrication: Reducing Friction in Processing
Improving Efficiency and Extending Equipment Life
Another significant role of Epoxy-modified Polyethylene Wax is as a lubricant in the processing of rubber and plastics. Lubricants play a crucial role in reducing friction during the manufacturing process, which can help extend the life of equipment and improve the efficiency of production lines.
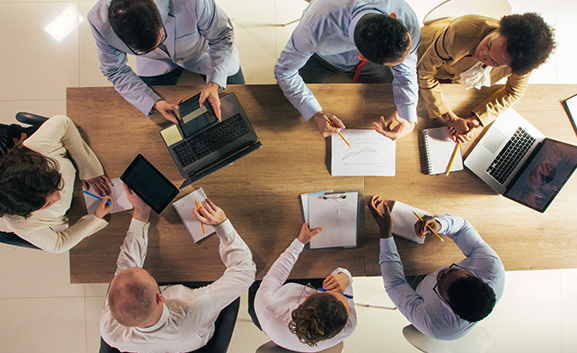
In rubber and plastic composite processing, Epoxy-modified Polyethylene Wax helps reduce melt viscosity, lowers extrusion pressure, and enhances the flow of materials. This, in turn, leads to smoother processing, less wear and tear on machinery, and better overall product consistency. Moreover, its high thermal stability ensures that it performs well even under high processing temperatures.
Enhancing Polarity: A Solution for Non-polar Resins
Increasing the Functional Capabilities of Non-polar Materials
Epoxy-modified Polyethylene Wax serves as a polarity enhancer, making non-polar resins like PE and PP more reactive and functional. These materials, by nature, have limited interaction with polar substances, which can reduce their performance in certain applications.
By incorporating Epoxy-modified Polyethylene Wax into the formulation, manufacturers can increase the polarity of non-polar resins, enabling them to bond better with polar materials such as pigments, stabilizers, or flame retardants. This increased polarity opens up new possibilities for improving the performance of PE and PP in applications requiring enhanced interaction with other materials.
Additional Functions of Epoxy-modified Polyethylene Wax
Versatility Across Industries
Epoxy-modified Polyethylene Wax also plays key roles in several other applications:
Adhesives: It is used in hot melt adhesives, composite films, and aluminum-plastic film industries, improving the bonding strength and durability of these products.
Anti-settling Agent: It acts as an anti-settling agent in coatings, preventing pigments and fillers from separating during storage and application.
Waterproofing Agent: It is also used in water-based coatings for paper, fiberboard, and wood, providing enhanced water resistance and improving durability.
UniVOOK Chemical: Your Trusted Supplier for Epoxy-modified Polyethylene Wax
Partnering with Industry Leaders for High-Quality Solutions
When looking for a reliable source of Epoxy-modified Polyethylene Wax, UniVOOK Chemical stands out as a trusted supplier. With a strong reputation in the chemical industry, UniVOOK Chemical offers high-quality GPW that meets the specific needs of manufacturers across multiple sectors. Whether you’re looking to improve compatibility in polymer blends, enhance the dispersion of pigments, or boost the performance of composite materials, UniVOOK Chemical provides expert solutions tailored to your requirements.
Conclusion: The Future of Polymer Processing with Epoxy-modified Polyethylene Wax
Epoxy-modified Polyethylene Wax is a versatile and indispensable tool in modern manufacturing, offering solutions to some of the most challenging issues in polymer processing. From enhancing compatibility and dispersion to improving thermal stability and mechanical properties, this modified wax has proven to be an essential additive for industries ranging from automotive to packaging.
As innovation in materials science continues to advance, Epoxy-modified Polyethylene Wax will remain at the forefront of the search for high-performance materials that meet the ever-growing demands of modern production. By partnering with leading suppliers like UniVOOK Chemical, manufacturers can ensure they have access to the best products to enhance their polymer systems and stay ahead of the competition.
Access Our Product Catalog and More to Discover High-Performance Chemicals Tailored to Your Business Needs