Best Maleic Anhydride Grafted Polyethylene Wax (MPEW) for Industrial Applications
What Makes Maleic Anhydride Grafted Polyethylene Wax Special?
In the world of polymer science, few materials boast the versatility and performance of Maleic Anhydride Grafted Polyethylene Wax (MPEW). By blending the robust, non-polar nature of polyethylene with the reactive, polar characteristics of maleic anhydride, this modified wax product offers unique properties that make it a game-changer in a variety of industries. The resulting material is not only an excellent coupling agent but also a versatile additive for improving product performance in countless applications. But what exactly makes MPEW so indispensable for manufacturers and industrial users?
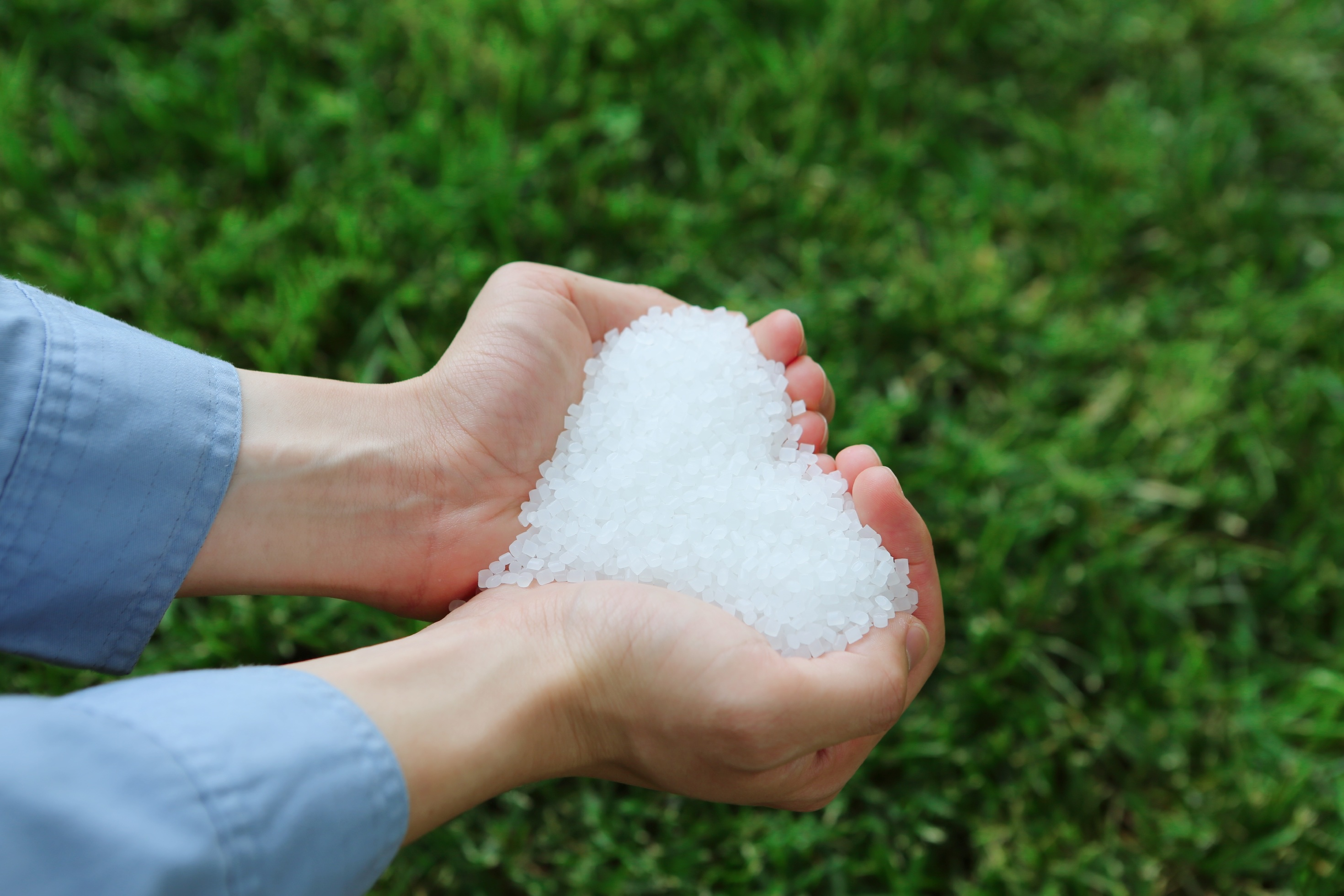
MPEW’s modified molecular structure, with both polar and non-polar properties, allows it to bridge gaps between different types of polymers, fillers, and resins. This fusion of characteristics provides enhanced compatibility, better adhesion, and improved processing efficiency, all of which play a critical role in optimizing the performance of a wide range of products. Whether it’s improving mechanical strength, enhancing dispersion, or providing better lubrication, MPEW is a go-to solution across industries such as plastics, rubber, coatings, adhesives, and more.
Versatile Applications Across Multiple Industries
Maleic Anhydride Grafted Polyethylene Wax is an incredibly versatile material that can enhance the properties of a wide range of products. Its ability to modify the behavior of different resins and materials makes it indispensable for multiple industrial sectors.
1. Coupling Agent in Polymer Composites
One of the most significant applications of MPEW is as a coupling agent in polymer composite production. When used in polyethylene (PE), polypropylene (PP), or polyvinyl chloride (PVC) processing, it improves the compatibility and adhesion between the polymer matrix and filler materials. In turn, this results in stronger, more durable composites with improved mechanical properties and thermal stability.
MPEW’s ability to act as a coupling agent allows manufacturers to achieve higher-performance materials by promoting a more effective interface between the filler and the polymer. This is especially valuable in the creation of composite materials used in automotive, construction, and packaging industries, where high-strength, lightweight, and heat-resistant materials are in high demand.
2. Dispersant for Masterbatch and Additives
Another key application of Maleic Anhydride Grafted Polyethylene Wax is as a dispersant in the production of masterbatches, including color masterbatches, flame retardant masterbatches, and degradation masterbatches. In the production of these materials, MPEW helps disperse pigments, dyes, and flame retardants more evenly throughout the resin, which significantly enhances the uniformity and color consistency of the final product.
For industries such as plastics, textiles, and packaging, MPEW ensures that additives like flame retardants are evenly distributed, preventing settling or clumping and improving the effectiveness of the flame retardants. This helps manufacturers deliver high-quality products with enhanced safety features, especially for applications in construction and electronics.
3. Compatibilizer for Multi-Polymer Systems
When it comes to creating complex materials that involve multiple types of polymers, achieving compatibility between different phases can be challenging. This is where MPEW acts as an efficient compatibilizer. It enhances the compatibility of matrix and dispersed phases in multi-polymer systems such as PE, PP, PBT, PET, PA6, and PA6/PC alloys.
By improving the interface strength between incompatible polymers, MPEW allows for the creation of multi-polymer alloys with superior properties. These alloys find extensive use in industries such as automotive manufacturing, where advanced composite materials are used to meet specific performance criteria, including toughness, flexibility, and heat resistance.
Performance Enhancements: Lubrication and Polarity Control
Maleic Anhydride Grafted Polyethylene Wax doesn’t just enhance material compatibility; it also offers lubricating properties that are highly beneficial in the processing of plastics and rubbers.
4. Lubrication in Rubber and Plastic Processing
MPEW’s role as a lubricant is especially important in the rubber and plastic composite processing industries. By reducing friction and enhancing flow during extrusion, molding, and other manufacturing processes, MPEW improves the efficiency and quality of the final product. This lubricant property ensures that materials can be processed at lower temperatures, which not only improves the overall productivity but also helps to preserve the integrity of the materials being used.
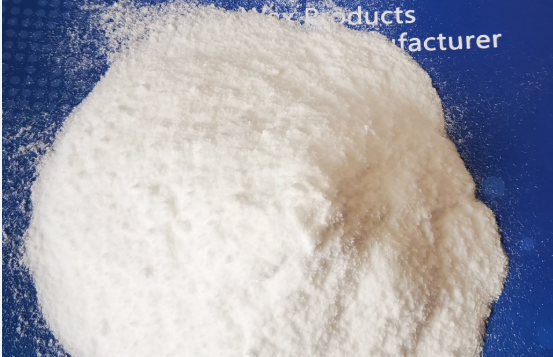
In rubber manufacturing, MPEW helps maintain the smoothness of the final product, preventing issues like uneven vulcanization or sticking during molding. The result is high-quality rubber and plastic products that meet stringent performance standards.
5. Polarity Enhancer for Non-Polar Resins
Another notable application of MPEW is its ability to act as a polarity enhancer. In its unmodified form, resins like PE and PP are highly non-polar, which can limit their compatibility with other materials that are more polar. MPEW overcomes this limitation by introducing polar maleic anhydride molecules into the polymer chain, which increases the polarity of the resin.
This increased polarity makes it easier to combine non-polar resins with other materials that have polar properties, resulting in more stable and durable products. Whether in the manufacturing of packaging materials, coatings, or adhesives, this property allows manufacturers to achieve superior results.
MPEW in Adhesives, Waterproofing, and Anti-Settling Applications
Beyond its role in enhancing polymers, Maleic Anhydride Grafted Polyethylene Wax has important applications in other industries, such as adhesives, coatings, and waterproofing.
6. Adhesives and Hot-Melt Applications
MPEW is widely used in the production of hot melt adhesives and composite films. Its excellent adhesion properties make it ideal for bonding applications in industries such as packaging, construction, and electronics. By enhancing the bond strength between different materials, MPEW ensures that adhesives are more durable and effective, even in challenging environments.
It is also used in the aluminum-plastic film industry, where it plays a vital role in improving the adhesion between the aluminum layer and the plastic film, ensuring that the films maintain their integrity and perform as expected in demanding applications.
7. Anti-Settling and Waterproofing Agent
MPEW is also an effective anti-settling agent in coatings and paints. In applications where pigment and filler particles tend to settle over time, MPEW helps prevent this by increasing the dispersion and stability of the particles. This property is particularly beneficial for water-based coatings and paints, as it ensures that the coating remains homogeneous and free from clumping or settling.
Additionally, MPEW’s ability to enhance water resistance makes it a key ingredient in waterproofing agents for various materials, including paper, fiberboard, and wood. By preventing water penetration, it helps extend the life and durability of these materials, especially in construction and packaging applications.
Why Choose UniVOOK Chemical for Maleic Anhydride Grafted Polyethylene Wax?
When it comes to sourcing Maleic Anhydride Grafted Polyethylene Wax, UniVOOK Chemical is a trusted and reliable supplier. With over 15 years of experience in the field of specialty chemicals, UniVOOK Chemical has established itself as a global leader in the production and distribution of high-quality industrial chemicals and biochemical materials.
Operating out of Shanghai, China, and with additional offices in Europe and Singapore, UniVOOK Chemical has the infrastructure and expertise to meet the diverse needs of customers around the world. The company’s state-of-the-art production facilities, coupled with a dedicated research and development team, allow UniVOOK Chemical to deliver customized solutions for a wide range of applications.
A Commitment to Quality and Innovation
UniVOOK Chemical is committed to advancing research, leveraging cutting-edge technology, and ensuring a high level of customer satisfaction. As an innovative and customer-focused company, UniVOOK works closely with its clients to develop tailored solutions that address specific industry challenges.
Conclusion: The Future of MPEW and Industry Solutions
Maleic Anhydride Grafted Polyethylene Wax is a material that continues to shape the future of many industries. With its diverse applications as a coupling agent, dispersant, lubricant, polarity enhancer, and much more, MPEW is an indispensable tool for manufacturers and industrial users. Whether you’re in the automotive, packaging, construction, or coatings industry, MPEW can elevate the performance and reliability of your products.
For businesses looking to enhance their manufacturing processes and achieve high-performance materials, partnering with UniVOOK Chemical offers access to a broad range of high-quality industrial chemicals and tailored services. With over a decade of experience and a focus on innovation, UniVOOK is the trusted supplier to help you stay ahead of the competition and bring your product visions to life.
Access Our Product Catalog and More to Discover High-Performance Chemicals Tailored to Your Business Needs