Oxidized Polyethylene Wax (OPEW): Global Market and Industrial Relevance
In today’s fast-evolving industrial landscape, many sectors are increasingly turning to specialized materials that enhance product performance and streamline manufacturing processes. One such material is Oxidized Polyethylene Wax (OPEW), a modified form of polyethylene wax that is synthesized through low-temperature catalytic oxidation technology. But why is this relatively obscure material gaining so much attention?
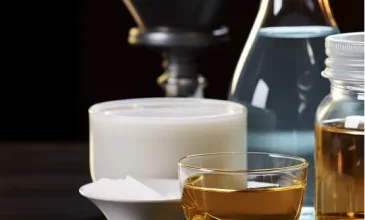
OPEW’s unique characteristics, such as its high softening point, hardness, and thermal stability, make it a highly valuable component in a range of industries. As we explore the global market for OPEW, we will uncover its increasing demand, the challenges faced by industries utilizing it, and the innovative solutions that are helping to overcome these obstacles.
Global Market Trends for OPEW: Rising Demand Across Industries
Oxidized Polyethylene Wax (OPEW) has emerged as a versatile material that can be applied in numerous industries. In recent years, the demand for OPEW has been expanding globally, driven by its wide range of applications in the plastics, rubber, inks, coatings, and masterbatch industries.
A Growing Demand for Performance-Enhancing Additives
The global market for OPEW is expected to see consistent growth as manufacturers continue to look for high-performance additives that can improve the properties of their products. According to industry reports, OPEW’s ability to serve as a lubricant, defilm agent, and viscosity regulator is making it an essential ingredient in the processing of materials like plastics, rubber, and paints. As industries continue to prioritize innovation and quality control, the adoption of OPEW is predicted to increase significantly, especially in emerging markets.
Increasing Adoption in Key Sectors
In the plastics and rubber industries, OPEW is used extensively as a dispersant, lubricant, and phase solvent. It ensures smoother processing and improved product quality, making it an invaluable raw material in the manufacture of color masterbatches, additives, and filling masterbatches. In the printing and coating industries, it is used as a brightener or anti-scratch agent, further enhancing the appeal of products. The expanding need for these features is largely contributing to the material’s growing adoption.
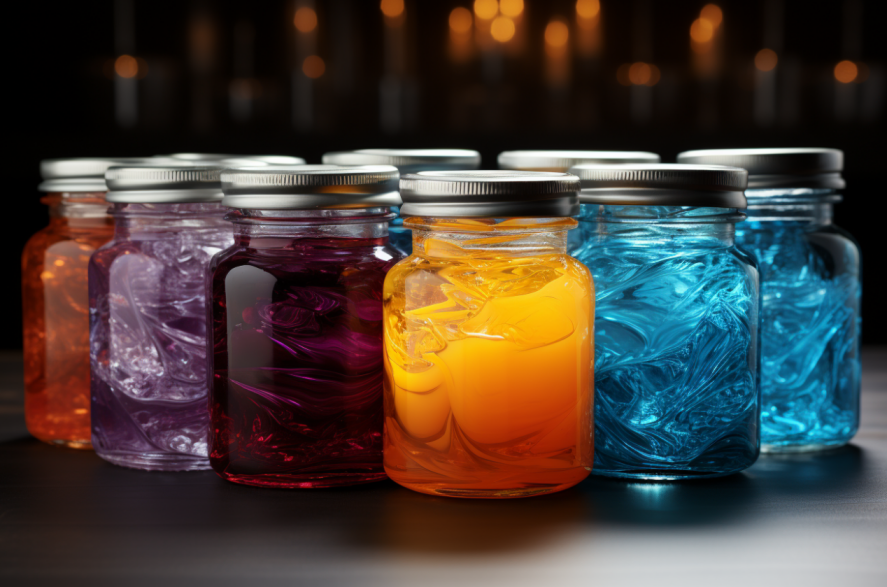
Industrial Challenges: Overcoming Hurdles in OPEW Utilization
Although oxidized polyethylene wax (OPEW) has many advantages. But using oxidized polyethylene wax (OPEW) in industrial applications is not without its challenges. As manufacturers and suppliers work to meet growing demand for OPEW. Several issues that may hinder its widespread adoption must be addressed.
Supply Chain Bottlenecks
One of the biggest challenges in the OPEW market is the complexity of supply chains. Since OPEW is extracted from polyethylene wax through a catalytic oxidation process. Therefore it is crucial to obtain a stable supply of high quality polyethylene wax. Any disruption in the raw material supply chain can lead to delays and price fluctuations. Thus affecting the entire production process. Additionally, transportation constraints and regional manufacturing differences can make it difficult for global industries to source OPEW at competitive prices.
Regulatory and Environmental Concerns
Another pressing challenge is the growing regulatory scrutiny surrounding industrial chemicals. As governments and organizations around the world pay increasing attention to environmental issues and sustainable development initiatives continue to advance. The production of chemical additives such as OPEW must meet stricter environmental standards. This has led to a demand for more sustainable production processes and materials that have a smaller carbon footprint. Companies need to ensure their OPEW production methods meet strict regulations. Otherwise they risk losing market access or facing legal consequences.
Variability in Product Quality
Because OPEW is produced through a low-temperature catalytic oxidation process, its final properties can vary significantly depending on the production method used. For example, while some manufacturers may produce OPEW with higher acid values for specific applications, others may focus on producing lower acid values for different purposes. This variability can make it difficult for manufacturers to ensure product consistency, leading to potential quality issues for end-users.
Solutions to Overcome Challenges: Enhancing Efficiency and Sustainability
To tackle the challenges faced by industries working with OPEW, companies and suppliers are focusing on a variety of strategies. From optimizing production processes to strengthening sustainability measures. We are implementing multiple solutions to ensure OPEW’s continued success in the global market.
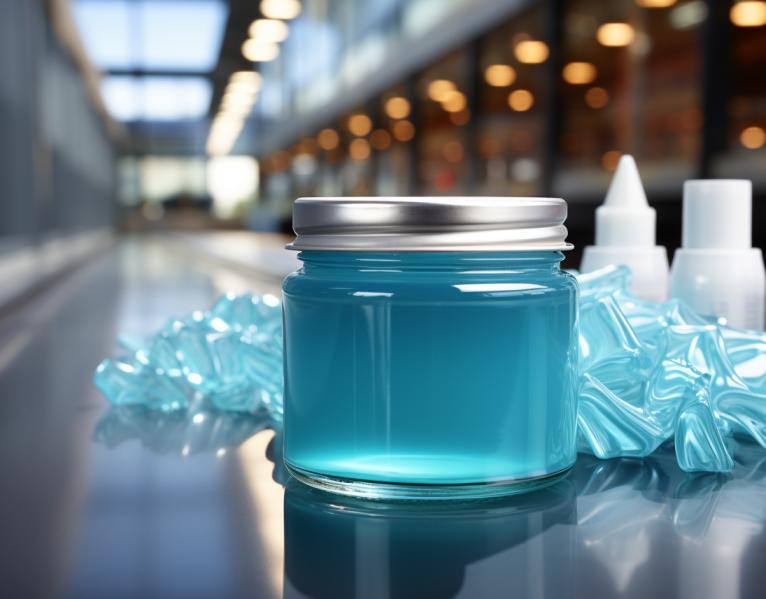
Optimizing Production Processes
To address supply chain challenges and improve production efficiency, many manufacturers are investing in more advanced technologies and automation. By streamlining production processes and leveraging cutting-edge equipment, manufacturers can reduce production time and costs while maintaining product quality. Additionally, adopting lean manufacturing techniques allows companies to minimize waste and optimize the use of raw materials, thereby increasing the sustainability of the OPEW production process.
Sustainable Production Initiatives
With growing concerns over environmental impact, many companies are shifting to more sustainable production practices for OPEW. For example, some manufacturers are exploring the use of biodegradable feedstocks or renewable energy sources to reduce the carbon footprint of their operations. The development of more sustainable catalytic oxidation methods can also reduce waste and emissions. These efforts align with global sustainability trends and help OPEW manufacturers stay competitive in an increasingly eco-conscious market.
Standardizing Quality Control
To combat the challenge of variability in product quality, companies are placing a strong emphasis on improving quality control measures throughout the OPEW manufacturing process. This includes using advanced testing techniques and implementing strict quality assurance protocols to ensure that the final product meets the required specifications. By ensuring consistency and reliability. Manufacturers can build trust with their customers and improve the long-term stability of their supply chains.
Conclusion: The Future of OPEW in a Dynamic Market
As industries continue to innovate and demand high-performance materials. Oxidized polyethylene wax (OPEW) is expected to play a key role in improving product quality and processing efficiency. Although challenges related to supply chain, regulatory compliance and product consistency remain. But manufacturers are looking for innovative solutions to address these issues and keep pace with the evolving market.
Global demand for multifunctional additives that improve the performance of plastics, rubbers, inks and coatings continues to grow. OPEW is expected to continue to be a key material in various fields. As leading Oxidized Polyethylene Wax (OPEW) suppliers like UniVOOK Chemical continue to push the boundaries of innovation, the future of OPEW looks bright, with new applications and solutions helping industries meet their evolving needs.
For companies seeking to explore the full potential of OPEW and other specialized materials, UniVOOK Chemical provides a wide range of high-quality solutions, including polymeric chain extenders, designed to meet the exacting demands of modern industries.
In conclusion, OPEW’s remarkable versatility, coupled with ongoing advancements in production and sustainability, ensures that it will continue to play a pivotal role in shaping the future of industrial manufacturing worldwide.
Access Our Product Catalog and More to Discover High-Performance Chemicals Tailored to Your Business Needs